Chip shortage: how can we cope with the global semiconductor shortage?
Table of contents
- The global shortage of semiconductors has created serious difficulties for the ICT, automotive, and consumer electronics sectors for several months. But what are the consequences for prices and lead times? And what strategies is Partitalia adopting to mitigate the risk?
- Chip shortage: the causes*
- Increased prices and lead times
- How are we mitigating this risk at Partitalia?
The global shortage of semiconductors has created serious difficulties for the ICT, automotive, and consumer electronics sectors for several months. But what are the consequences for prices and lead times? And what strategies is Partitalia adopting to mitigate the risk?
The shortage of electronic components, or chip shortage, as it is called, can be traced to many events that have occurred since late 2019.
Chip shortage: the causes*
• Covid-19 and factory shutdowns
The onset of the COVID-19 pandemic in early 2020 resulted in a temporary shutdown of factories, leading to a general economic slowdown. Major global players in the automotive sector — the leading market in the semiconductor industry — started cancelling orders placed with chip manufacturers in January and February 2020. Foundries therefore reduced their production, and the spread of the virus forced them to close their factories for weeks at a time, with an unavoidable reduction in stocks.
• Smart working and distance learning increase the demand for consumer electronics
Meanwhile, in February and March 2020, the spread of smart working and distance learning led to an exponential increase in the purchase of consumer electronics — computers, tablets and smartphones — needed to cope with new work and school requirements. This surge in demand for consumer electronics, which had never occurred before, was so large that it also covered the automotive market.
A few months later, between July and September 2020, the automotive factories started up again, albeit gradually. The sum of these factors led to a considerable increase in demand for semiconductors. Indeed, the demand was so high that supplies were insufficient and factories experienced an unprecedented crisis.
• The Renesas factory fire and the water crisis in Taiwan
The situation was further aggravated by the trade war between China and the US and the fire at the Renesas Electronics factory in Tokyo — one of the world’s leading semiconductor manufacturers — in March 2021. At the same time, Taiwan — home to TSMC, the world’s largest semiconductor factory — was hit by a severe drought that led to water rationing, forcing factories to use trucks for water supplies. This further slowed down productivity.
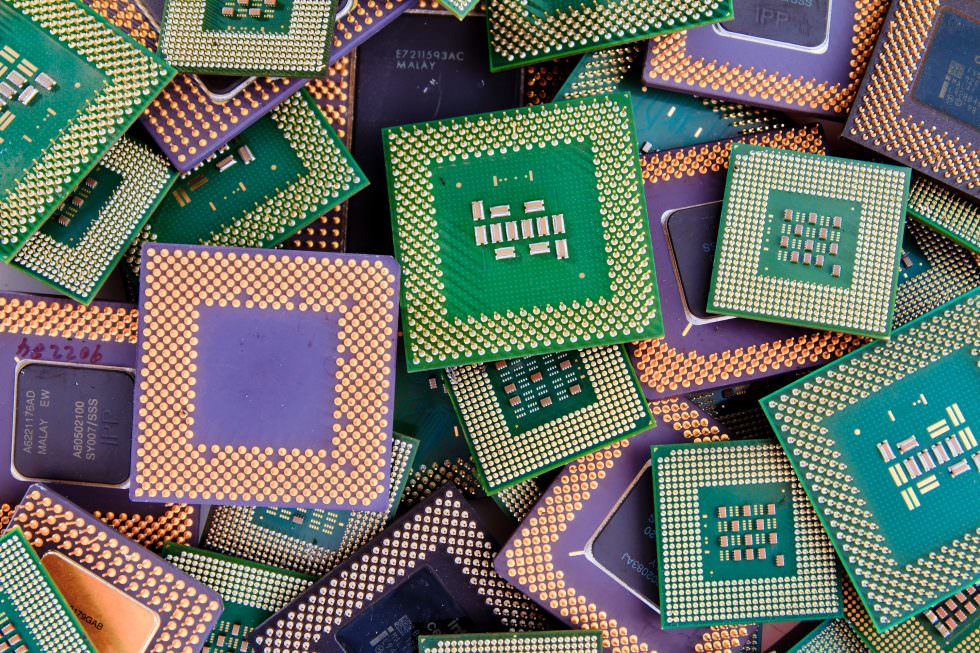
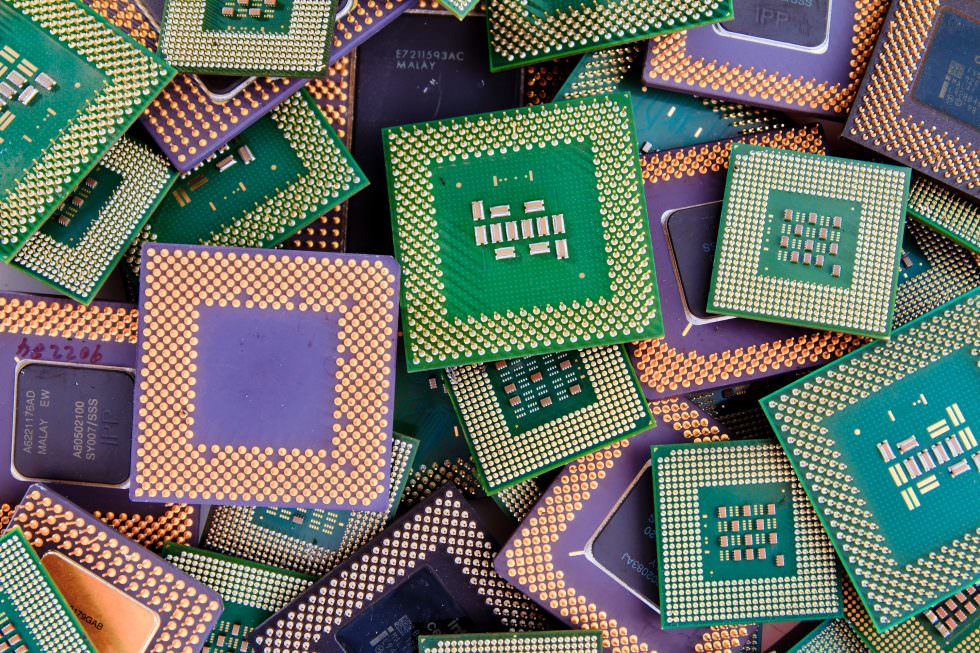
Increased prices and lead times
One of the main consequences of the chip shortage was an increase in costs by suppliers, who are producing more profitably, as confirmed by Gartner, a US strategy consulting firm, in a press note last May: ‘Foundries are increasing wafer prices and, in turn, chip companies are increasing device prices,’ explains Kanishka Chauhan, principal research analyst at Gartner.
The note reads: ‘The global semiconductor shortage will persist throughout 2021, and is expected to return to normal levels by the second quarter of 2022’ (source: Gartner Says Global Chip Shortage Expected to Persist Until Second Quarter of 2022).
Delivery times from suppliers have increased and prices are rising with a subsequent increase in lead times, the time between the customer’s request and the company’s delivery of the product. The solution is certainly not to change brands, since building a factory from scratch takes at least four years, as well as huge investments.
How are we mitigating this risk at Partitalia?
To avoid delivery delays or production cancellations, in Partitalia we have increased our stock. We also place preorders to have greater protection on future supplies.
To improve service quality, we ask you for twelve-month rolling forecasts, with bimonthly reviews. Our sales team is ready to support you in this activity.
* In partnership with Paolo Sala, Field Sales Engineer at Red Tree Solutions