The most common material used to produce cards — credit/debit cards, fidelity cards and supermarket loyalty cards, ID badges for access control at companies, hotels, gymnasiums, and so on — is PVC
The PVC, polyvinyl chloride, is a thermoplastic polymer consisting of 57% sea salt and 43% crude oil and is widely used in an extensive range of industrial and technical applications, the disposal of PVC nevertheless causes major environmental problems. Indeed, if incinerated, it releases dioxins and other organochlorines into the atmosphere.
In the Green Paper ‘Environmental Issues of PVC’ presented in Brussels by the European Commission in June 2000, we read: ‘Upon incineration, PVC waste generates hydrochloric acid (HCl) in the flue gas, which needs to be neutralised.’
Hence, the need arose to market a material that is less polluting and more respectful of the health of both the planet and humans. At the beginning of the new millennium, the European PVC industry joined the 10-year Vinyl 2010 programme to make the entire product supply chain more sustainable by reducing the environmental impact of production, promoting the responsible use of additives and supporting recycling programmes. VinylPlus was launched in 2011. This new ten-year European programme for the sustainable development of PVC brings together some 200 partner companies representing the entire supply chain (converting companies, producers of raw materials and additives, recyclers).
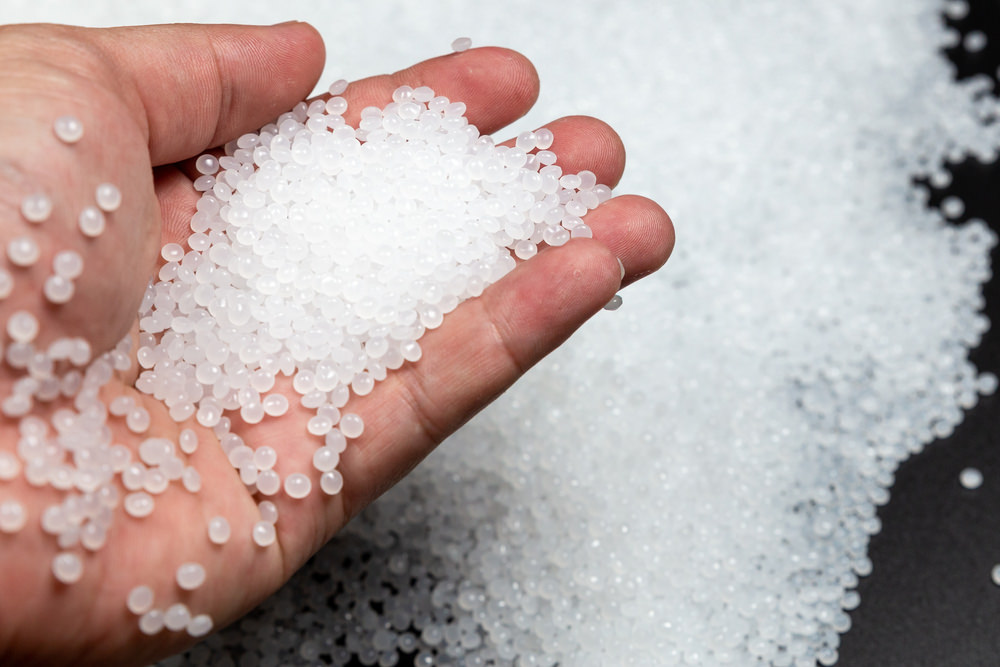
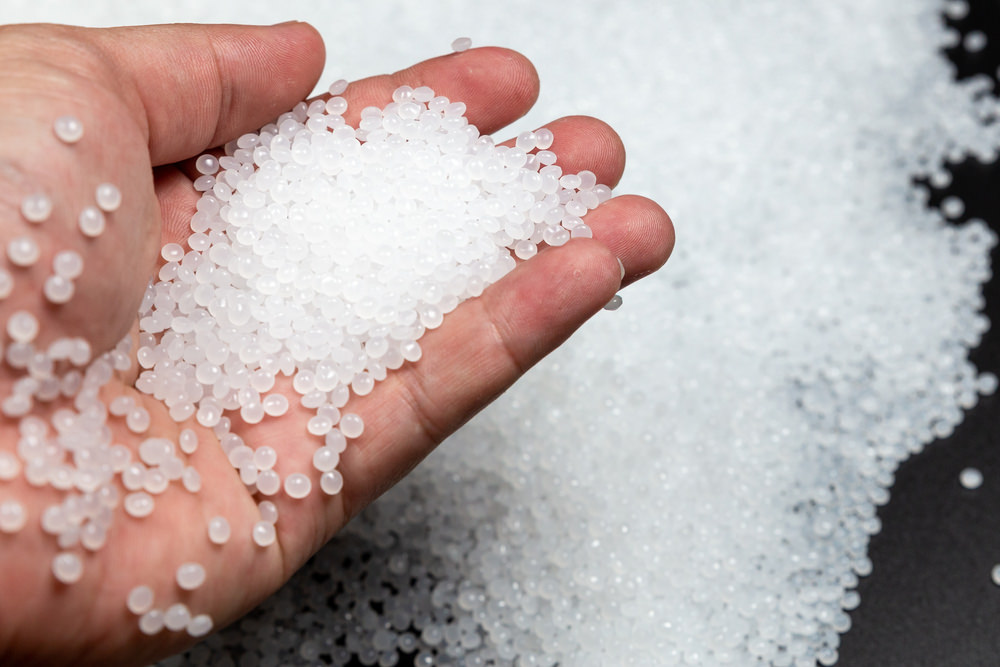
Degradable PVC and recycled PVC: green alternatives to standard PVC
Two more-sustainable alternatives to standard PVC currently on the market are degradable PVC and recycled PVC.
Degradable PVC
Degradable PVC is made using additives that accelerate its degradation in microbe-rich environments, such as biologically active landfills.
The additives are particularly ‘palatable’ to microorganisms — fungi, bacteria, algae — normally found in rubbish. They recognise these markers and secrete acids that metabolise the substances found in PVC, breaking the molecular chain and converting the polymer into simple molecules (water, carbon dioxide, methane), biomass and inorganic compounds. Hence, throwing degradable PVC cards in the wet waste bin facilitates their degradation by the bacteria found in organic waste.
According to standard UNI EN 13432:2002, ‘Requirements for packaging recoverable through composting and biodegradation’, plastics must decompose by at least 90% in less than six months to be defined as biodegradable.
Degradable PVC Cards: which is the market trend?
Given their small size, cards may seem to have a minimal environmental impact; in reality, however, they are widely used — just think of how many people carry credit cards, office and gym ID badges, and various loyalty cards issued by supermarkets and shops.
Today, an increasing number of industrial groups have a cleaner view of the world and are adopting more planet-friendly behaviour. Hence, more companies are requesting degradable PVC cards to promote the environmental sustainability of their products and comply with European guidelines, with advantages in terms of visibility and marketing as well.
Which are the changes from a technical point of view?
PVC is widely used not only for cards, but also to produce pipes, window frames, packaging for food and medicine, and insulation film due to its outstanding technical features:
- printability;
- durability;
- flexibility;
- high chemical resistance;
- optimal temperature resistance;
- electrical insulation;
- impermeability.
From a technical point of view, degradable PVC retains the same characteristics as the standard material.
Moreover, with the same technical performance, degradable PVC offers unquestionable advantages in terms of environmental impact. Indeed, it breaks down much faster than the traditional material — already in the wet waste and then in landfills without releasing dioxin or other harmful organochlorines generated in the combustion process.
Through its Research and Development team, Partitalia, a leader in the smart card market since 2003, is constantly searching for innovative materials — via technical laboratory and eco-compatibility tests — to develop products that meet customer needs with respect for the planet.