S.I.BE.G. Ltd has chosen Partitalia’s “Close-to-me” devices at its plant in Catania and at the CCBS plant in Tirana, a company in the same group. We interviewed Gaetano Russo, Procurement Manager at S.I.BE.G. Ltd.
Interview with Gaetano Russo, Procurement Manager at S.I.BE.G.
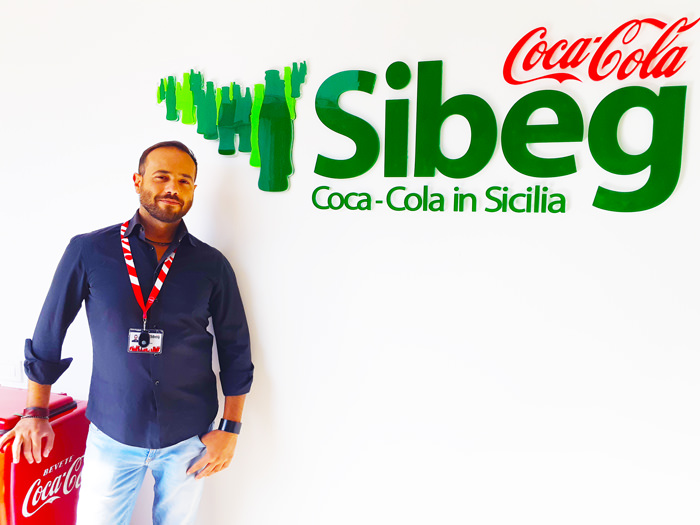
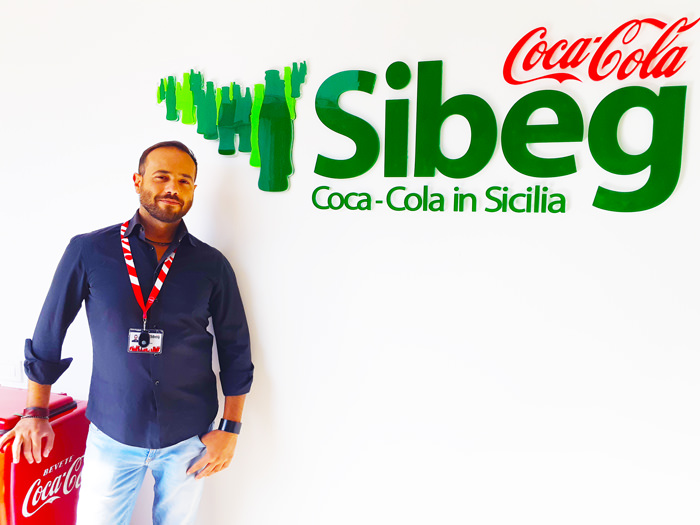
What is S.I.BE.G. Ltd involved in?
«S.I.BE.G. Ltd since 1960 has been the “The Coca-Cola Company’s” soft drinks’ bottling company in Sicily. Today the company has 350 employees at its Catania plant from which between 30 and 100 trucks of soft drinks are sent out every day to more than 30,000 sales points throughout Sicily. At the site in Catania there are the headquarters with the offices and the production plant which has six bottling lines to cover all the formats: tin cans, glass bottles, PET bottles and on tap systems.
In Sicily today, S.I.BE.G. Ltd is not only synonymous with Coca-Cola, but also with sustainability. The company is mindful of the impact of its production on the environment. For this reason it has taken action to reduce its ecological footprint and is a total green energy company: in 2016 it entered into an agreement with Enel under which all the electric power used for production comes from 100% renewable sources. In addition, the company has installed a 189-kilowatt photovoltaic system on the roof of the plant in Catania that supplies 10% of our energy requirement.
We have also developed the Green Mobility project: an important project launched in 2015 and thanks to which S.I.BE.G. has become the company with the largest fleet of fully electric vehicles in Europe. With around 110 fully electric vehicles assigned to our Sales Executives, our Field force, every year, 363 tons of Co₂ are saved and not emitted into the atmosphere: this is almost equivalent to the quantity of Co₂ absorbed by 27,000 trees, that correspond to a forest covering an area of 34 football fields! Finally, in 2020 we installed a trigenerator to produce 45% of the plant’s total energy requirements. In this way we will save even more Co₂».
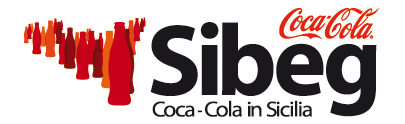
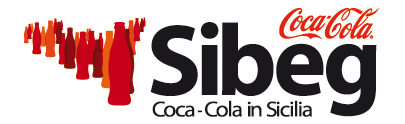
How did you get in contact with Partitalia?
“We came across Partitalia completely by chance. In March, at the peak of the Covid-19 emergency, the company set up a task force to define and implement appropriate safety measures, including the indispensable adoption of a system that would help us observe social distancing rules. So we searched on all possible channels: a member of our staff, the manager of the IT department, came across one of Partitalia’s adverts and immediately passed on the information. We contacted Partitalia and spoke to them about our needs; in the end, from among the various players in the sector we chose Partitalia and its “Close-to-me” device».
Why did you choose “Close-to-me”?
«There were many reasons why we chose “Close-to-me” over the other devices of competitor companies. The approach of the Partitalia staff that followed our project certainly played a fundamental role: they were so helpful, and we created an excellent rapport immediately. They listened to our needs, assimilated them and then proposed the most appropriate bespoke solutions.
We needed a simple but effective device, something that would remind employees and everyone present in the plant to keep a distance of one and half/two metres from each other. We needed something that was light to wear, an acoustically non-invasive device but which performed this function. Above all, we also needed a software that could rapidly provide reports about contacts between devices to be able to reconstruct the history of the contacts, above all in the case of a confirmed case of Covid.
“Close-to-me” is a small device that can be worn around the neck all day and is not an annoyance. It warns wearers acoustically when it comes into contact with another device but it is not too noisy. Moreover, it is connected to a software, with which we can download the entire history of each device it has come into contact with at a distance of less than one and a half metres. These are the winning features of “Close-to-me”: other devices on the market are larger and at times use more advanced technologies than we actually need.
Last but not least, the low cost of this device compared to those of all the other competitors on the market. The price is certainly inviting compared to that of the other devices proposed.
We tested the device for a couple of weeks, asking for a few sample devices which we received immediately. We chose these devices for the S.I.BE.G plant in Catania and for the plant in Albania, in Tirana, another “Coca-Cola” bottler in the same group».
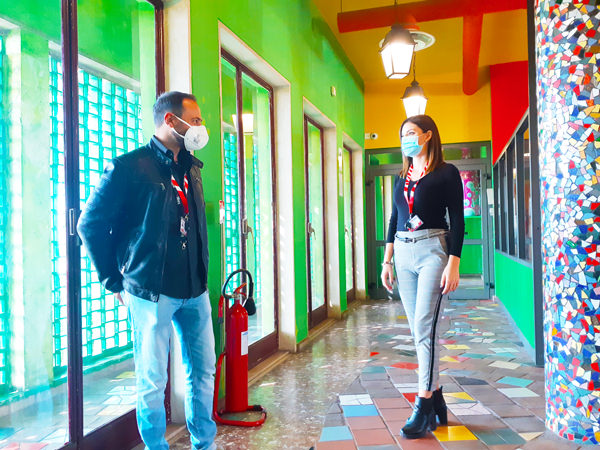
How many devices are you using? How are you getting on? Do you have any other numbers?
«We bought a total of 300 “Close-to-me” devices for the Catania plant and around 250 for Albania.
At present at S.I.BE.G. Catania we used 200 for our employees, each of whom has been associated with a personal device that they bring with them to work, switching it on at the start of the shift and switching it off when they leave at the end of the shift. The other 100 are used for visitors entering the plant and who, before entering, must hang it around their neck, switch it on and then return it when they leave.
We are satisfied with our choice in the sense that the device does exactly what it was designed to do, warning us when the distance between people is less than one and a half metres».