Four fundamental points help to frame the Industry 4.0 phenomenon: the use of data as a tool to create value (big data); the extraction of value from collected data (analytics); the human-machine interaction; the transition from digital to real in the form of produced goods and services.
Up to a few years ago, very little was said of Industry 4.0 in public discussions and even less in daily life conversations, at least in our country. However, the expression rapidly became established and is now on the tip of many people’s tongues. A popularity that grew rapidly, especially after the entry of Industry 4.0 onto the political scene and the debate generated by government decisions.
Speaking of Industry 4.0 may perhaps be fashionable, but the phenomenon is not necessarily distinguished by clarity of ideas on what is really meant by it.
Industry 4.0: definition
The name Industry 4.0 can be explained as a reference to the industrial revolutions that have brought about an acceleration in the history of modern western civilisation. In this sense, Industry 4.0 evokes a fourth industrial revolution after the introduction of the steam engine (1784), the introduction of electricity (1870) and the advent of electronics and IT (which can be placed at the end of the sixties and start of the seventies in the 20th century). The basic idea of 4.0 is that a profound change in the way of producing and using goods and services is in progress. A change that can also be defined as “Digital Revolution”. The result of this revolution in progress, with enormous economic, social and cultural consequences, will be represented by factories where the machines will be constantly interconnected; they will be capable of self-diagnosis and resolving problems that may arise during the production process. A model that we are rapidly approaching can be encapsulated in the English expression “smart factory” or “smart manufacturing”. If you move from factories to homes and all the contexts of people’s daily lives, you can more generally speak of “smart living”.
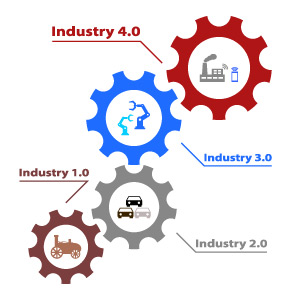
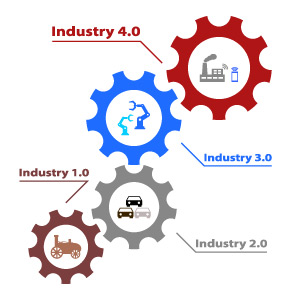
The first step towards Industry 4.0
The western country that can be considered the homeland of Industry 4.0 is Germany.
The expression Industry 4.0 was used for the first time in 2011 at an electronics fair hosted by the city of Hanover. The next year, in October 2012, a work group submitted a list of recommendations to the German government to modernise the production system in the framework of “Industrie 4.0” (as it is called in German). The final report, aimed at steering and supporting enterprises during the profound transformation destined to emerge in the fourth industrial revolution, was presented during the Hanover fair in April 2013 and helped Germany confirm itself, in a European context, as the leading country in the path towards the full realization of the idea of Industry 4.0.
Industry 4.0 in Italy
In our country Industry 4.0 made its institutional début in November 2015, when the Ministry for Economic Development announced the document “Industry 4.0, the Italian way for manufacturing competitiveness. How to make the digital transformation of industry an opportunity for growth and employment”. A plan for Industry 4.0 was entered by the Italian government in the Budget Act of 2017. The plan, which put 30 billion euros in research and development on the table, aimed to stimulate private investment with tax incentives for companies, support the spread of ultra-broad band and network security and promote the training of skilled personnel and make the range of Industry 4.0 applications known. However, it is widely thought that Italy, both in the results of the institutional efforts and the capacity of the citizens’ perception, is behind in the possibility of fully grasping the meaning and the opportunities associated with Industry 4.0.
How Industry 4.0 works
Four fundamental points can help to give a picture of Industry 4.0: the use of data as a tool to create value (big data); the extraction of value from the data collected (analytics); man-machine interaction; the passage from digital to real in the form of goods and services produced. Industry 4.0 optimizes the computerization of the production process which was already a feature of Industry 3.0. Now, computers can not only communicate with each other but they are also capable of taking decisions without the involvement of human intelligence. With the progressive acquisition of data, the “intelligent machines” are becoming ever more intelligent, making the production process ever more efficient and less subject to wastes and various types of risks. Just think of the possible negative consequences, for different types of companies, of a sudden change in the atmospheric conditions, which can be perfectly forecast thanks to machines connected to the network. An example of how Industry 4.0 can offer considerable advantages for entrepreneurs, but also for their employees who find themselves facing risks from a health point of view.
The predictive maintenance entrusted to machines connected to the network can prevent accidents to plants; a smart device worn by a worker belonging to a risk category can, by communicating data on his/her physical condition to the network, even save his/her life. This is one of the sectors where Partitalia is investing in research and development and already counts important references.
In terms of market composition, Industry 4.0 in Italy sees three large components: the most significant is the Industrial IoT, with approximately 790 million euros of turnover in 2015 and is 66% of this market. The IoT equipment, intelligent sensors and infrastructures are part of this component: Industrial Analytics is undoubtedly the second fundamental component of the sector with 23% and 270 million euros of turnover generated in 2015. The circle is closed with Cloud Manufacturing which represents 10% of the total pie and concerns Industry 4.0 projects that are cloud supported for a value in 2015 of 120 million euros.
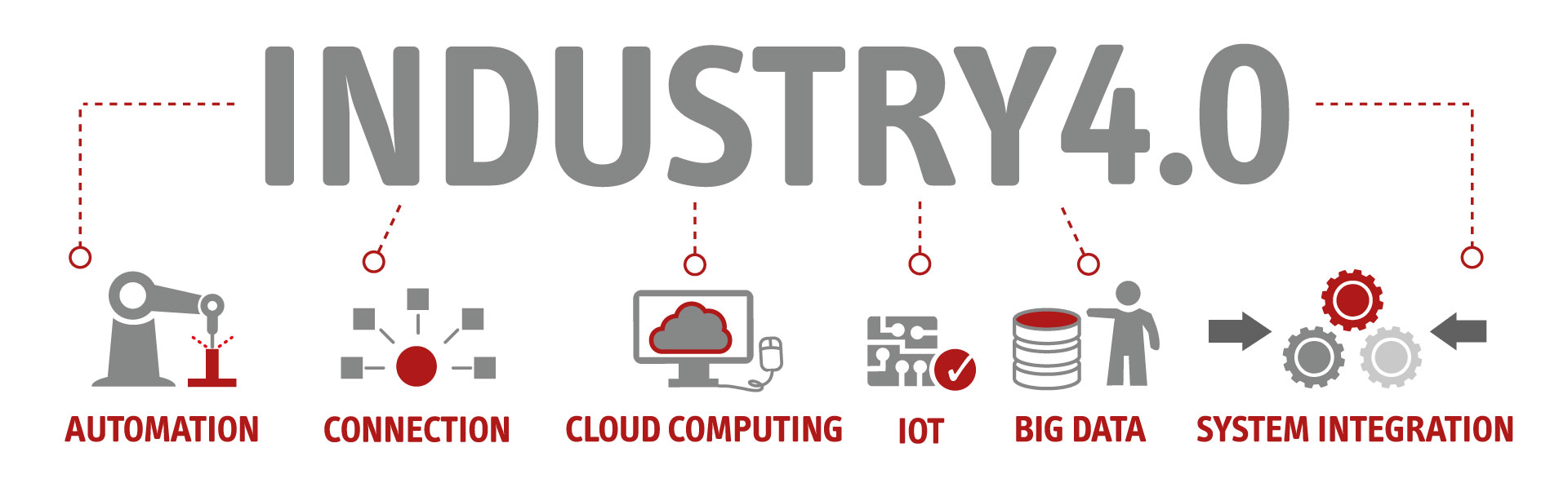
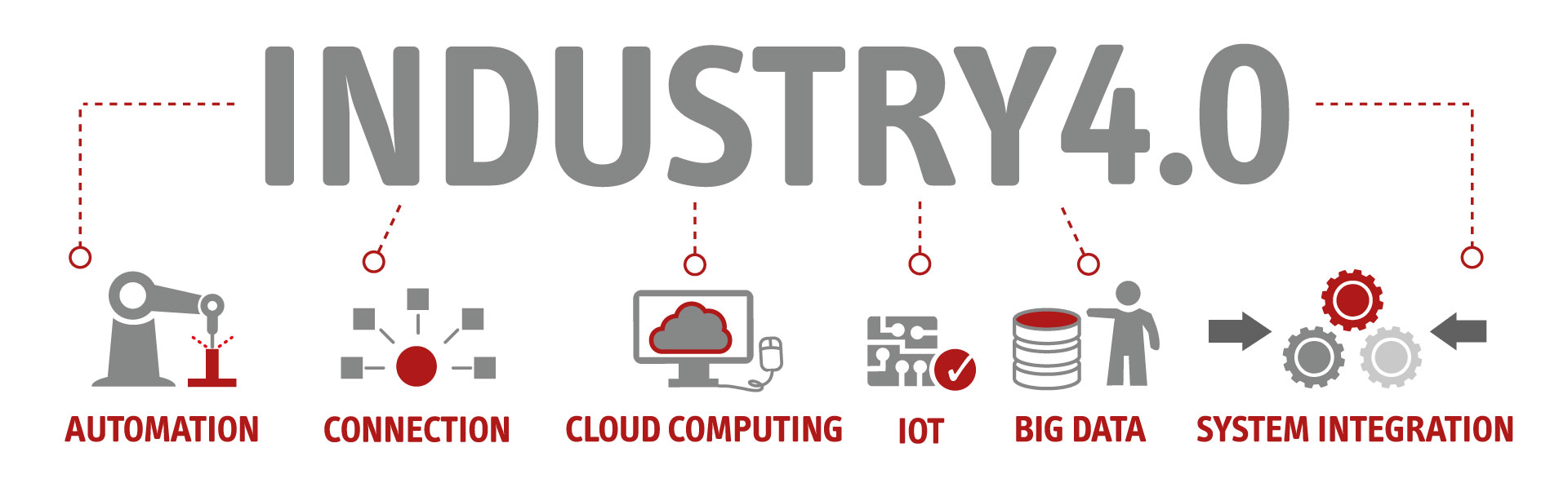